verope® betreibt die ersten zwei Dauerbiegemaschinen weltweit, die nach einem neuen, revolutionären Konzept gebaut wurden. Das Drahtseil wird in die Prüfmaschine eingebaut und belastet und läuft dann so lange über fünf Seilscheiben hin und zurück, bis es in der Seilmitte reißt. Erst dann beginnt die Analyse des Drahtseils: Auf der linken und auf der rechten Seite der gebrochenen Seilzone, die während des Versuchs über fünf Scheiben hin und zurück gelaufen ist, befinden sich zwei Seilzonen, die nur über vier Scheiben gelaufen und nicht bis zur fünften gekommen sind. Unabhängig davon, welche Bruchbiegewechselzahl im Versuch erreicht wird, haben diese Zonen immer genau 80% dieser Biegewechselzahl ertragen. Diese Zonen und die weiteren Zonen, die nur über drei, zwei, eine oder über gar keine Scheibe gelaufen sind und somit die Seilzustände nach 60%, 40%, 20% und 0% der Seillebensdauer repräsentieren, werden nun für die weitere Untersuchung herausgeschnitten (Abb. 35).
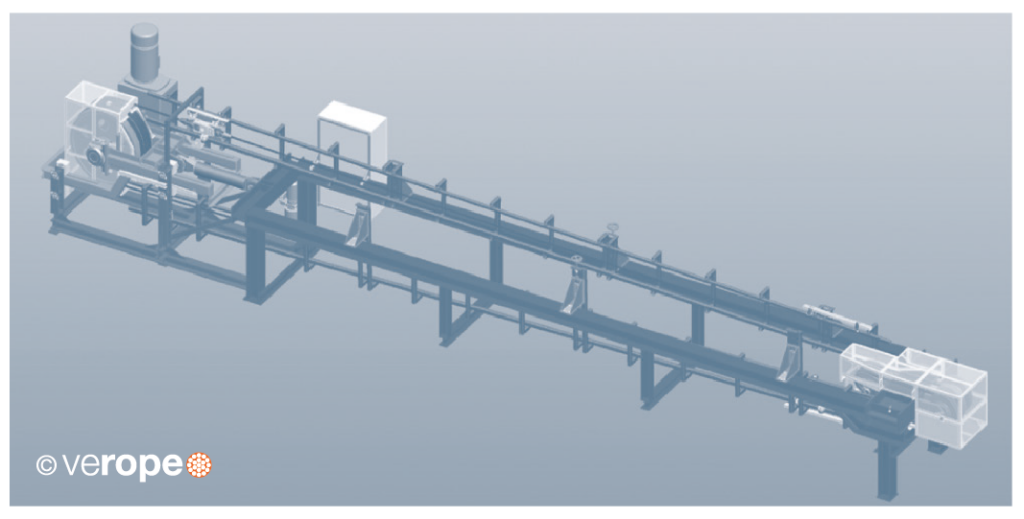
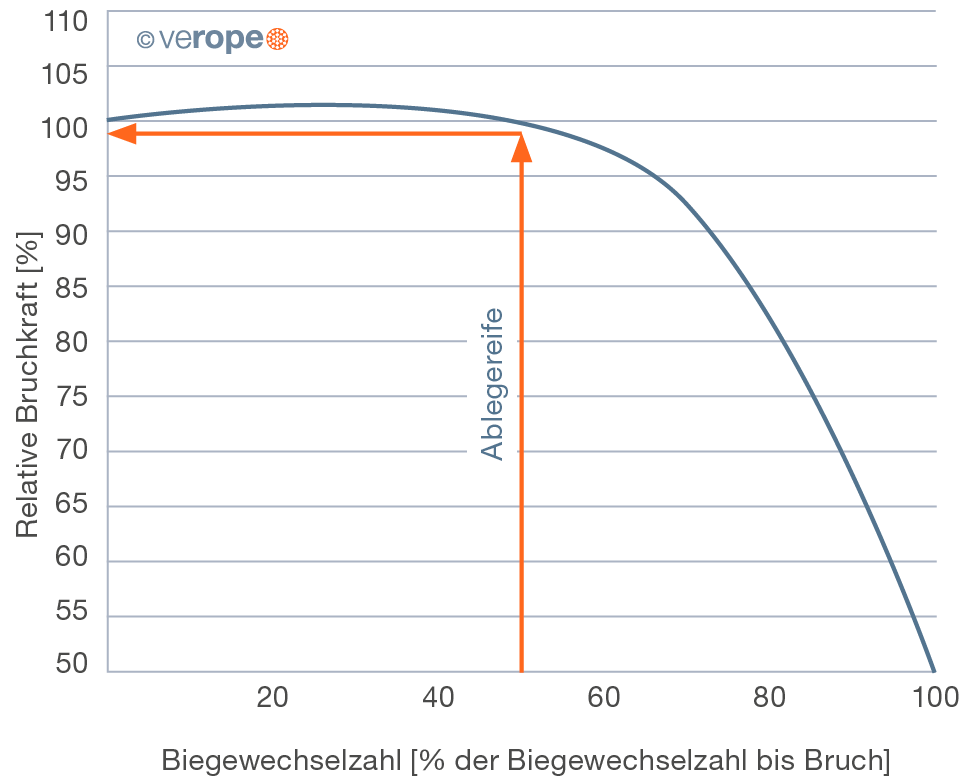

Auf diese Weise kann man ermitteln, wie sich die äußeren Drahtbrüche während der Lebensdauer des Seiles entwickeln, wie sich die inneren Drahtbrüche im Laufe der Lebensdauer entwickeln, wie sich eine Kunststoffzwischenlage während der Seillebensdauer verändert und welche Seilelemente als erste versagen. Diese Resultate helfen verope®, die Qualität seiner Produkte zu überwachen oder die Geometrie eines neu entwickelten Seiles bereits nach dem ersten Versuch deutlich zu verbessern. Die vergleichbaren 80%-, 60%-, 40%-, 20%- und 0%-Zonen auf der anderen Seite der Bruchstelle werden einem Ganzzerreißversuch unterworfen. Auf diese Weise kann verope® ermitteln, wie sich die Bruchkraft, der Elastizitätsmodul und die Bruchdehnung seiner Produkte über der Lebensdauer des Seiles verändern. Ein Drahtseil sollte bei Erreichen der Ablegedrahtbruchzahl eine Bruchkraft aufweisen, die noch etwa so hoch oder sogar noch höher ist als im Neuzustand (Abb. 34).
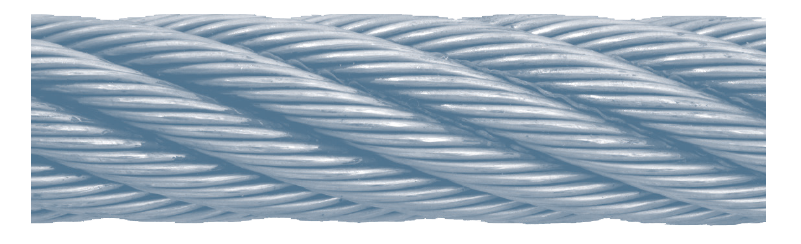
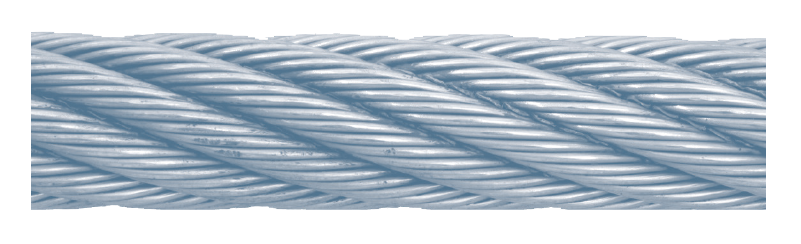
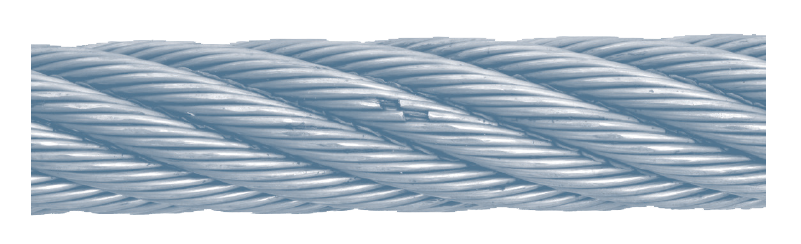
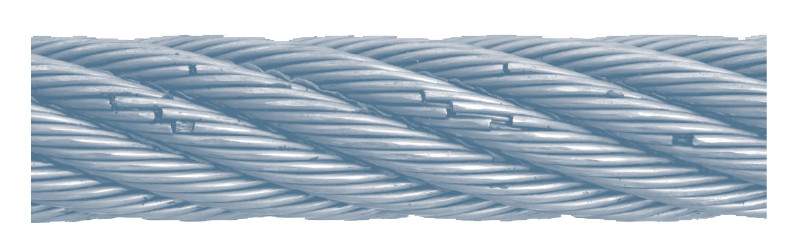
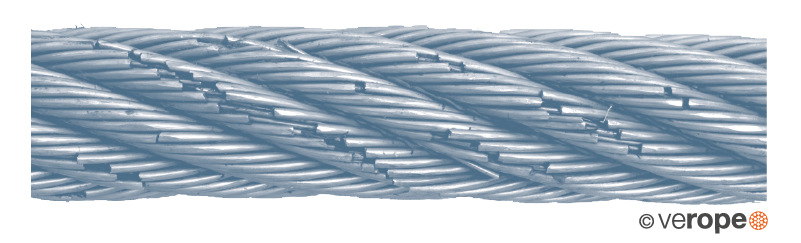
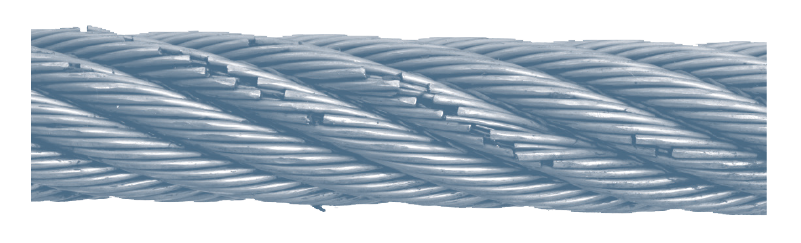
Die Seilzonen, die beim Dauerbiegeversuch über keine, eine, zwei, drei, vier oder fünf Seilscheiben laufen, zeigen nach Versuchsende (Seilbruch) den Zustand des Seiles bei einer Biegewechselzahl von 0%, 20%, 40%, 60%, 80% und 100% (Seilbruch) an. Durch die detaillierte Analyse der einzelnen Arbeitsbereiche ist der Verlauf der sichtbaren Drahtbrüche über der Seillebensdauer sehr genau zu bewerten (Abb. 42).
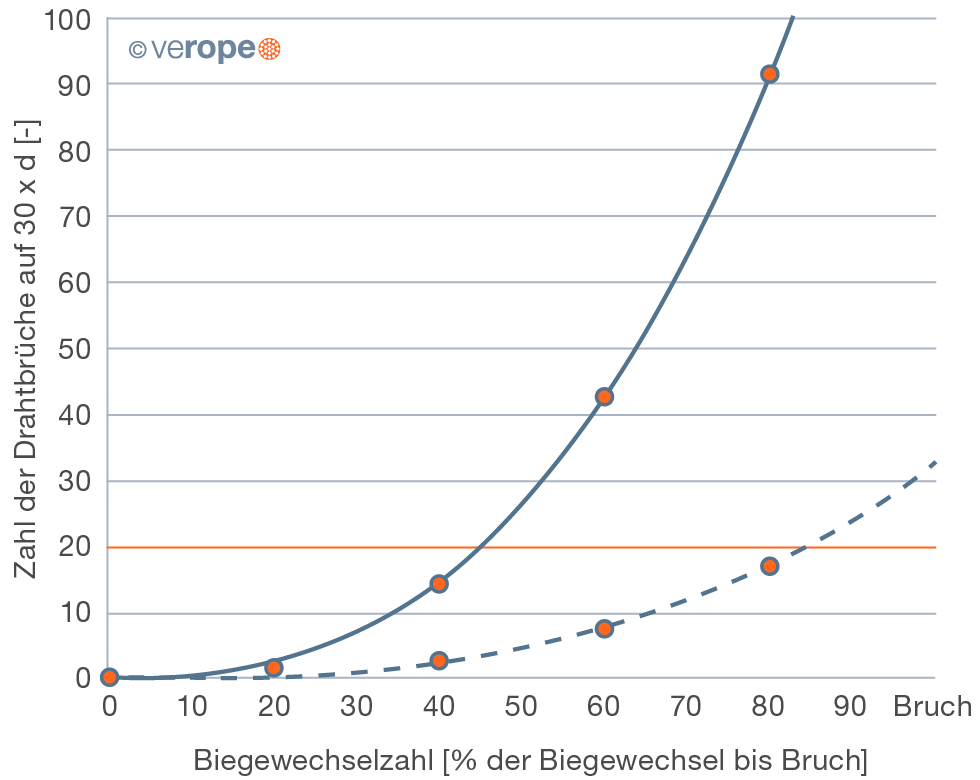
Nach dem Zerlegen der Seilstücke können auch die im Seilinneren auftretenden Drahtbrüche in Abhängigkeit von der Seillebensdauer ermittelt werden (Abb. 43). Bei der Konstruktion veropro 8 ist die Anzahl der sichtbaren Drahtbrüche höher als die nicht sichtbaren.
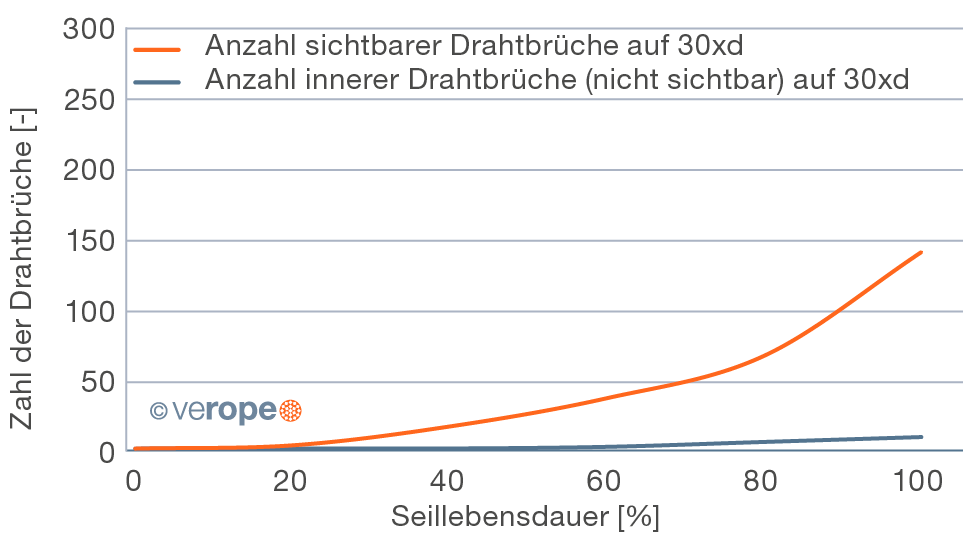
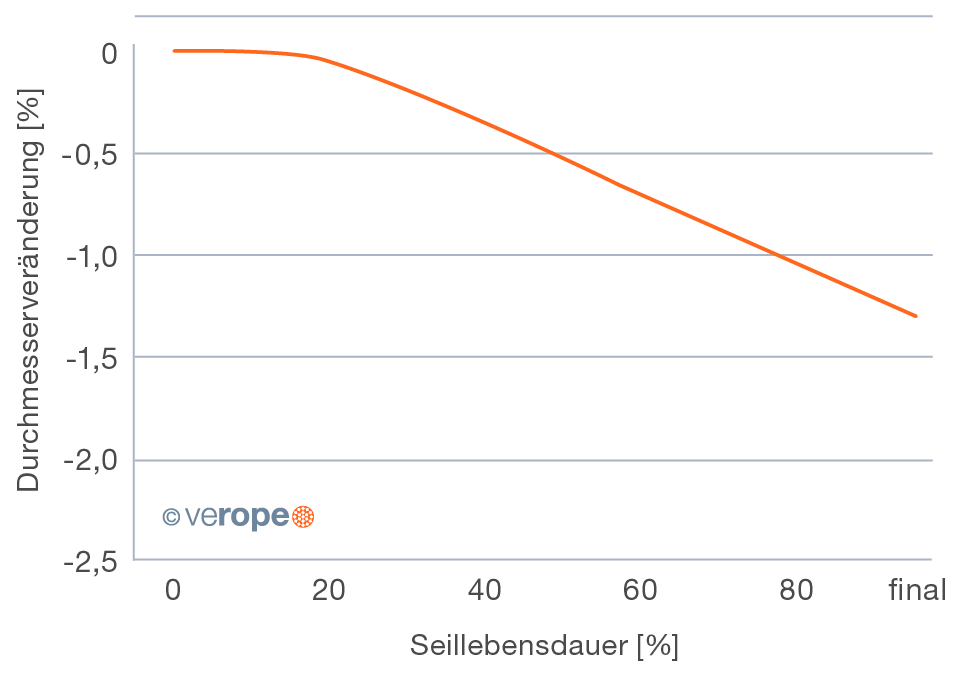
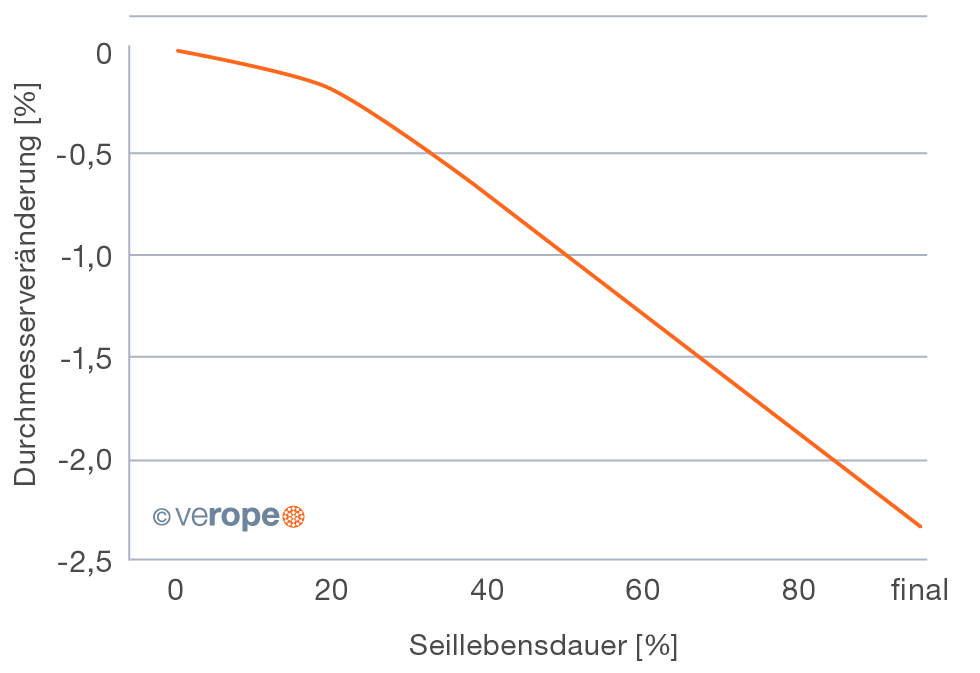
Biegewechselversuche werden standardmäßig bis zum Bruch einer Litze bzw. des Seiles durchgeführt. Durch das Auswerten der einzelnen Seilsektionen kann der genaue Punkt der Ablegereife bestimmt werden. Hieraus ergibt sich auch die so genannte Restlebensdauer (die Lebensdauer zwischen Ablegereife und Bruch) (Abb. 46).
Abb. 47 zeigt einen Vergleich der Biegewechselzahlen bis zum Erreichen der Ablegereife nach ISO 4309 sowie bis zum Bruch für nicht drehungsfreie Seilkonstruktionen unter gleichen Versuchsbedingungen.
Abb. 48 zeigt einen Vergleich der Biegewechselzahlen bis zum Erreichen der Ablegereife nach ISO 4309 und bis zum Bruch für drehungsfreie Seilkonstruktionen unter gleichen Versuchsbedingungen.
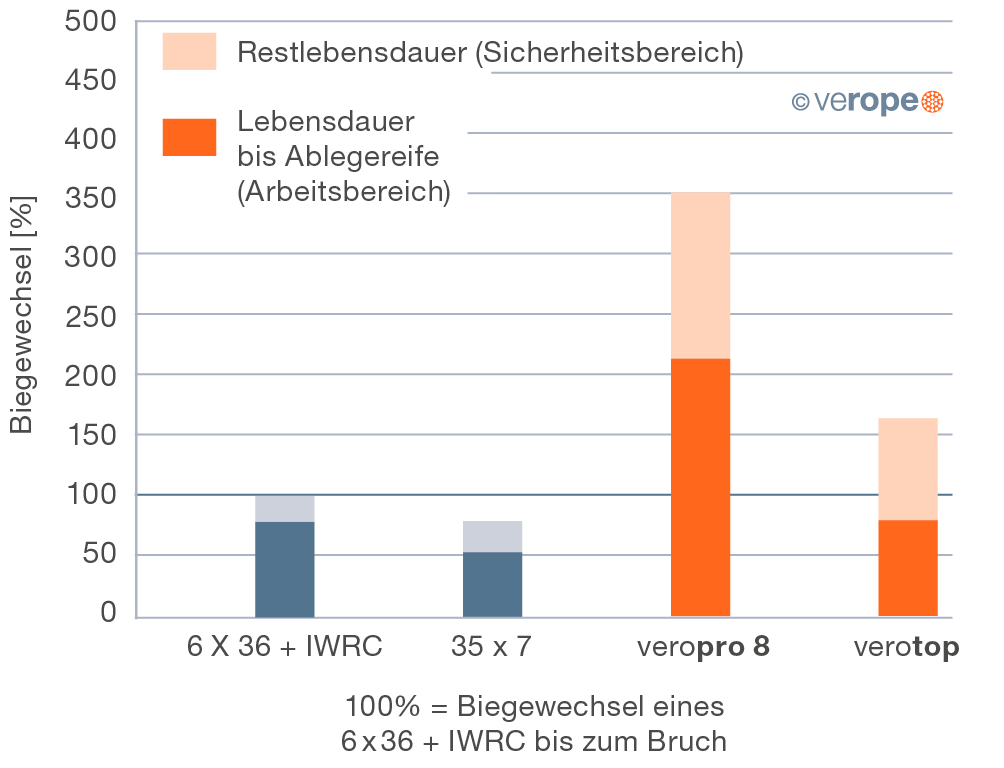
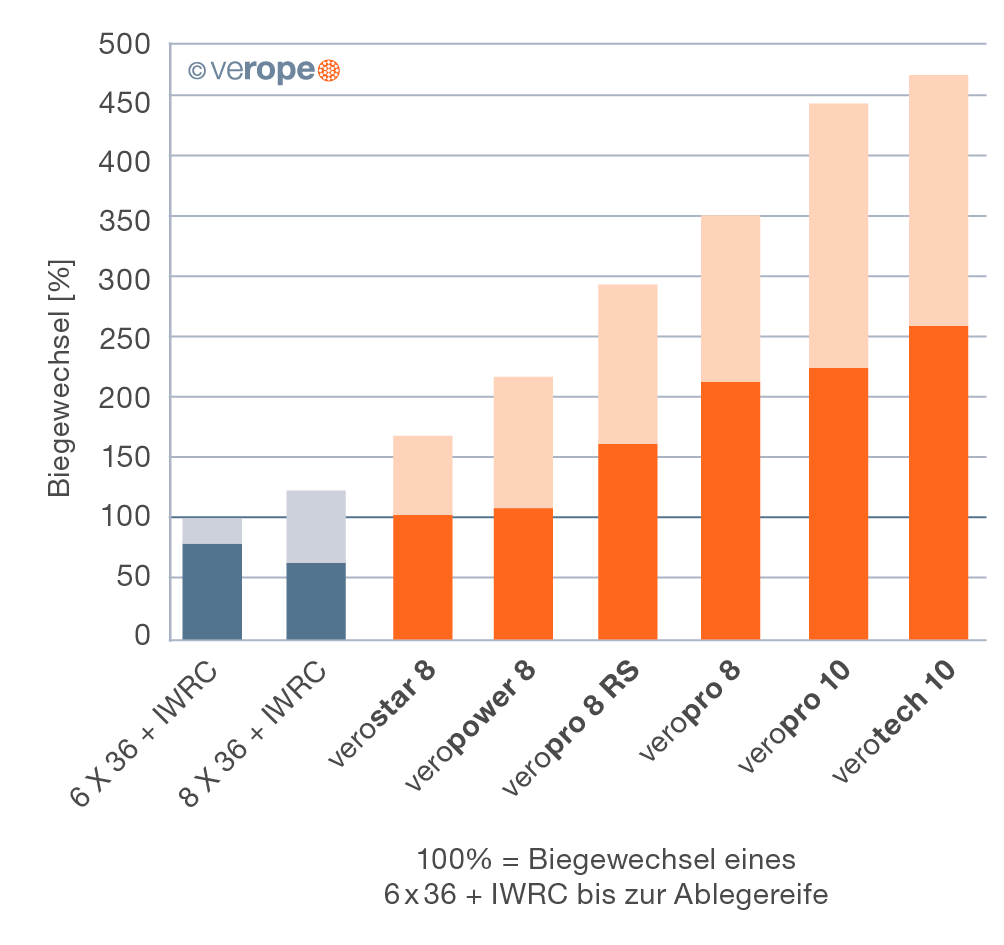
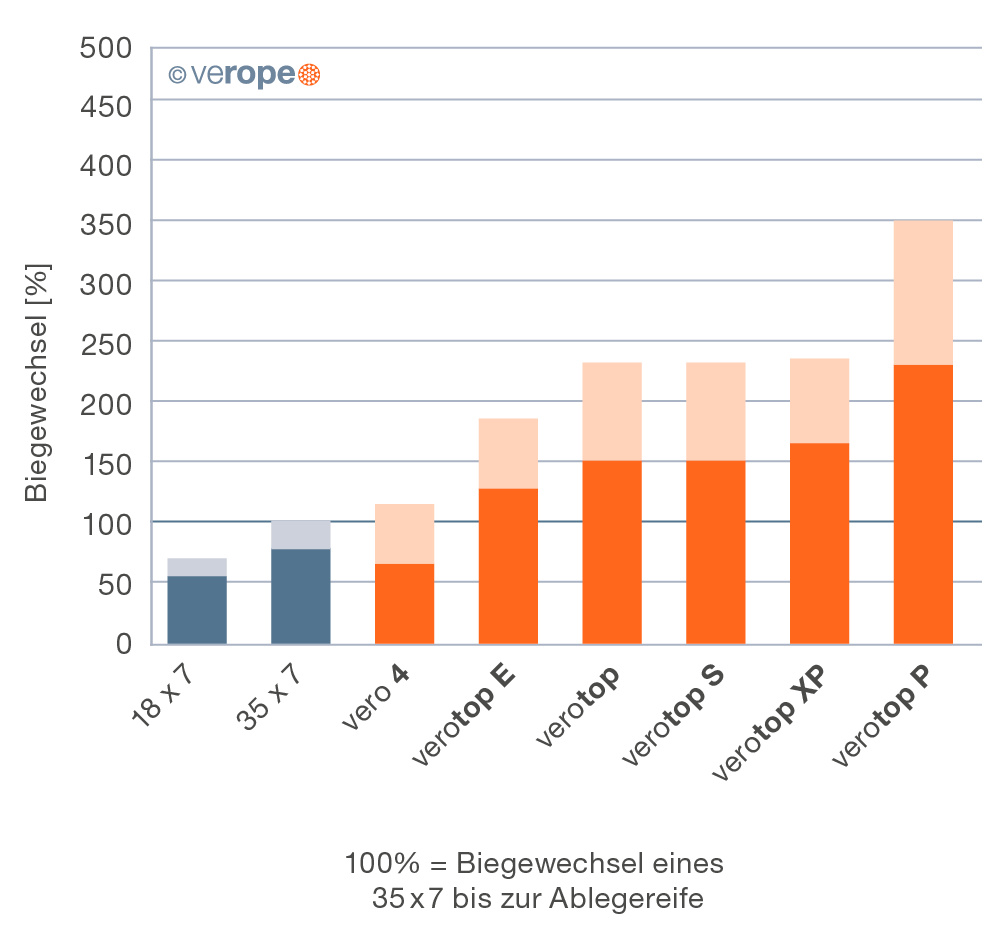
Seillebensdauer bei Verwendung von Stahlscheiben und Kunststoffscheiben
Die Seillebensdauer wird durch den Scheibenwerkstoff deutlich beeinflusst. Bei Verwendung von Kunststoffscheiben steigt die Biegewechselleistung im Vergleich zu Stahlscheiben deutlich an. Die verbleibende Seilrestlebensdauer nach dem Erreichen der Ablegereife bis zum Bruch des Seiles ist, bezogen auf die Anzahl der Biegewechsel, in etwa gleich, sinkt jedoch prozentual deutlich ab (Abb. 49). Somit muss bei der Verwendung von Kunststoffscheiben die Seilinspektion besonders sorgfältig durchgeführt werden. verope® empfiehlt Kunststoffscheiben daher nur für Anwendungen, wo die Seile magnetinduktiv geprüft werden, oder für Anwendungen, wo die Seile im Wesentlichen außen beschädigt werden, wie z.B. bei der Mehrlagenwicklung.
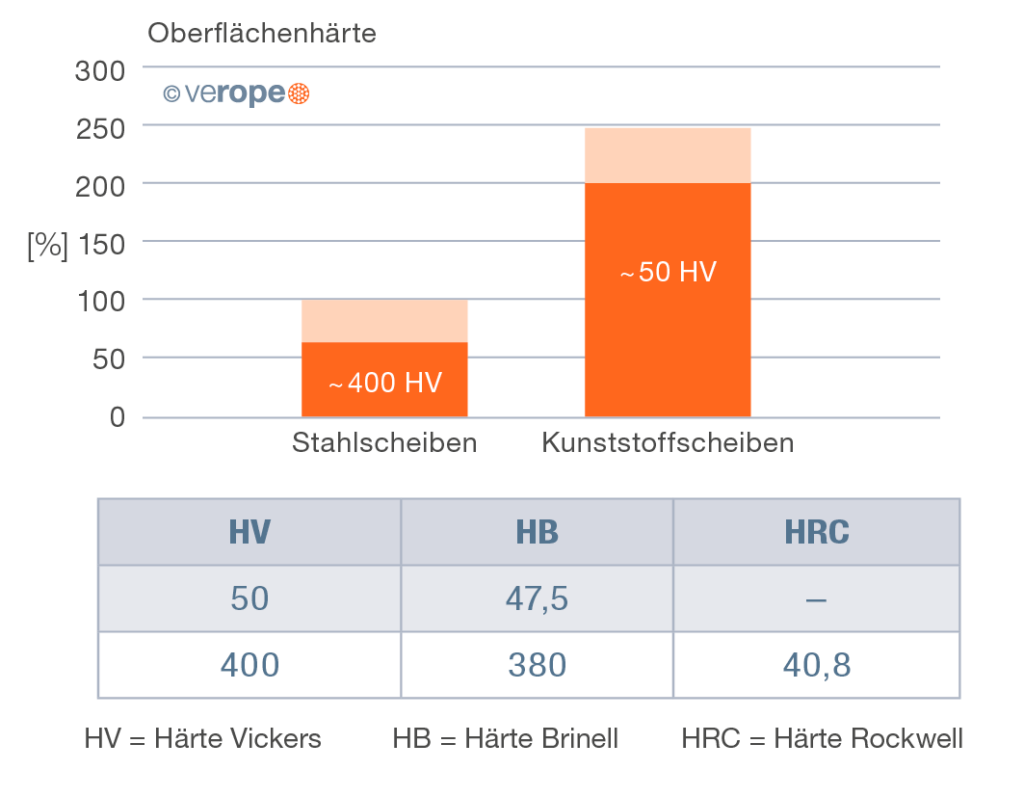
Seillebensdauer von blanken und verzinkten Seilen
Ein Vergleich der Biegewechselzahlen von blanken und verzinkten Seilen bis zum Erreichen der Ablegereife nach ISO 4309 und bis zum Bruch zeigt, dass verzinkte Seile in der Regel höhere Lebensdauern erreichen (Abb. 50). Die Zinkauflage bietet bessere “Notlaufeigenschaften” bei verbrauchtem Schmiermittel und schützt vor Reibkorrosion.
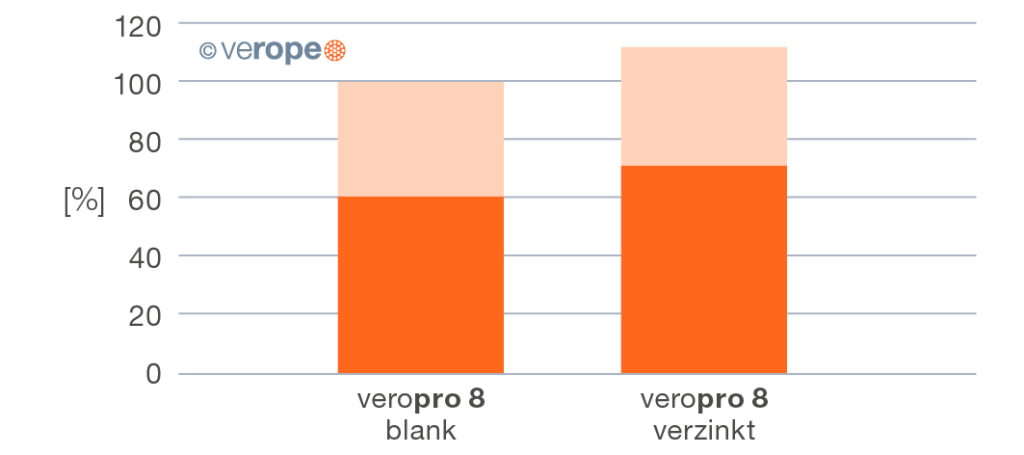
Seillebensdauer in Abhängigkeit vom Rillendurchmesser
Nach ISO 16625 sollte die Rille der Seilscheibe einen Durchmesser besitzen, der 5 bis 10 % größer ist als der Seilnenndurchmesser. Im Laufe der Einsatzzeit wird sich der Seildurchmesser verringern. Das Seil wird sich mit diesem verringerten Durchmesser in die Seilscheibe eingraben und den Rillendurchmesser verkleinern. Deshalb sollte bei der Montage eines neuen Seiles beachtet werden, dass der Rillendurchmesser der Seilscheiben mindestens 1% größer ist als der gemessene Seildurchmesser. Bei zu großem Rillendurchmesser wird das Seil weniger gut unterstützt, und die Flächenpressung erhöht sich. Folglich reduziert sich die Seillebensdauer mit zunehmendem Rillendurchmesser stetig. Ist hingegen der Rillendurchmesser zu klein, wird das Seil gezwängt, und die Seillebensdauer fällt extrem ab.
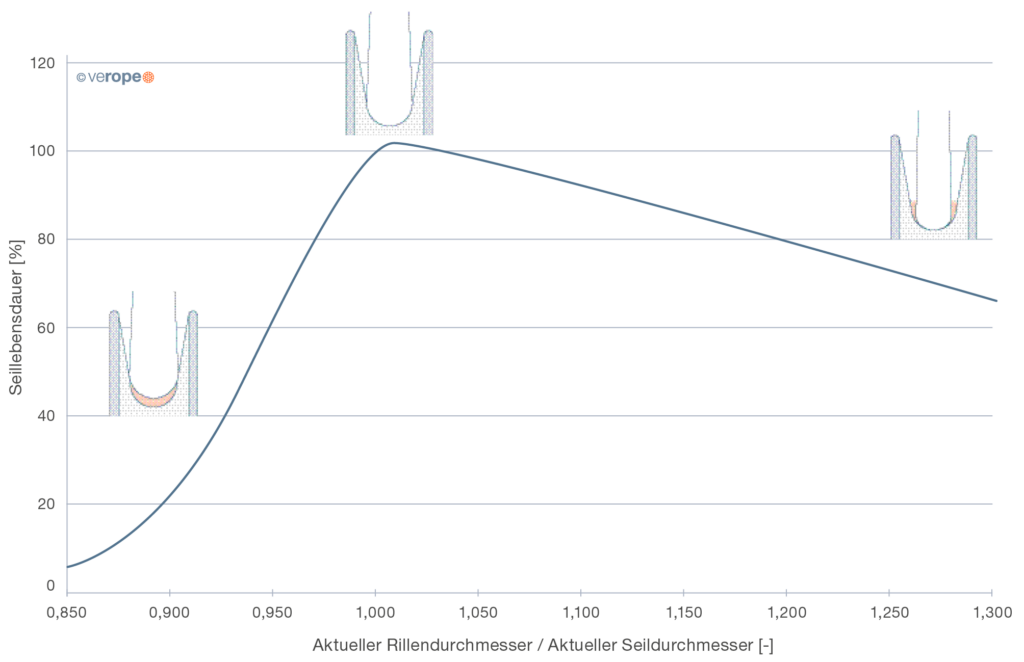
Seillebensdauer in Abhängigkeit von der Stranglast
Die einwirkende Stranglast hat erheblichen Einfluss auf die Seillebensdauer. Während beispielsweise bei einer Stranglast von 2 t noch 950.000 Biegewechsel erreicht werden, werden bei einer Stranglast von 4 t nur noch 290.000 Biegewechsel erreicht (Abb. 52).
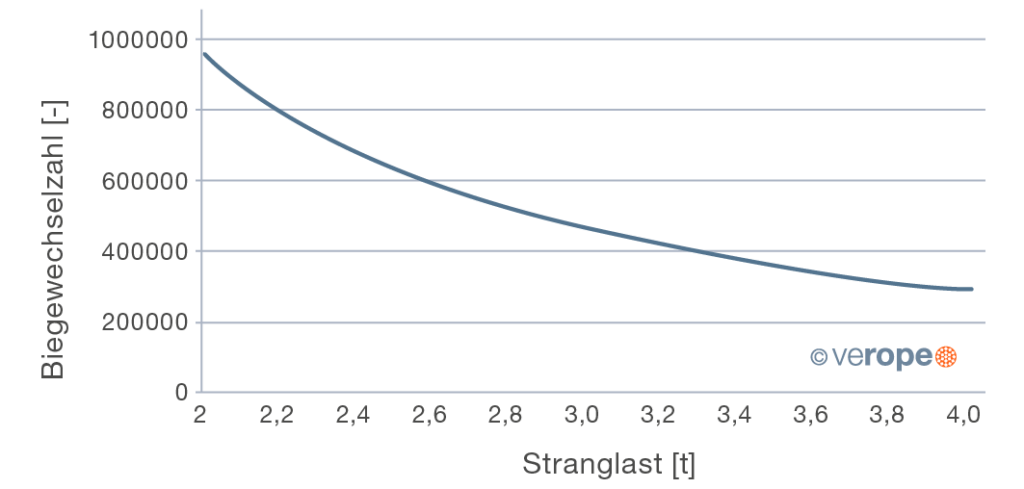
Seillebensdauer in Abhängigkeit vom Scheibendurchmesser
Die verwendeten Durchmesser von Seilscheiben und Seiltrommeln beeinflussen die Seillebensdauer deutlich. Während beispielsweise ein Seil beim Lauf über eine Seilscheibe mit einem Durchmesser von 800 mm noch über 2.000.000 Biegewechsel erreicht, reduziert sich die Biegewechselleistung durch Halbieren des Scheibendurchmessers auf 400 mm auf 290.000 (Abb. 53).
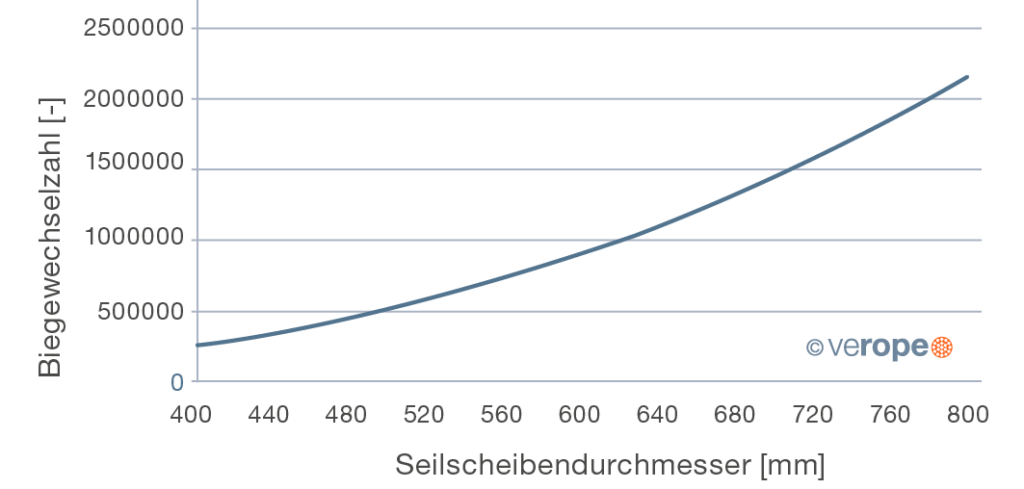